Comprehensive Guide to Effective Product Packaging Machine Repair Work Methods for Optimal Efficiency
Efficient packaging maker repair is crucial for maintaining functional continuity and item quality in today's fast-paced production atmosphere. Utilizing an organized approach to diagnostics and repair service, along with preventative upkeep approaches, can significantly enhance device durability and performance.
Typical Packaging Equipment Concerns
Product packaging devices, necessary for efficient assembly line, usually run into several usual problems that can interrupt procedures. One widespread trouble is misalignment, which can lead to improper labeling or sealing, inevitably influencing item stability and discussion. This imbalance may stem from worn-out components or improper setup throughout initial installment.
One more regular concern is irregular product packaging speeds, usually triggered by mechanical wear or not enough maintenance. Variability in speed can lead to bottlenecks, creating delays and minimizing overall efficiency. Additionally, inadequate training of workers can exacerbate these concerns, as operators may not totally recognize device performances or fixing techniques.
In addition, material jams are a typical incident, usually as a result of inaccurate material specifications or foreign things blocking the maker's path. Such jams can stop production, demanding immediate treatment to get rid of the blockage and resume operations.
Lastly, electronic faults, consisting of software glitches or sensor failings, can hamper maker capability - packaging machine repair service. These issues need prompt interest, as they can result in extensive downtime otherwise dealt with without delay. Understanding these usual concerns is crucial for keeping optimal performance and minimizing interruptions in packaging operations
Diagnostic Methods for Repair Work
Carrying out effective analysis strategies is critical for determining and settling issues in packaging makers. A systematic strategy to diagnostics allows specialists to determine the source of malfunctions successfully, consequently minimizing downtime and improving functional efficiency.
Among the primary methods involves visual assessments, where technicians take a look at the machine for any apparent signs of damages, misalignment, or wear. This fundamental step can often expose crucial concerns without the requirement for innovative devices. Making use of analysis software can considerably enhance the troubleshooting process. These devices assess maker efficiency information, supplying understandings right into abnormalities that may not be instantly noticeable.
An additional vital strategy is conducting functional examinations. By systematically running numerous components of the maker, service technicians can observe efficiency inconsistencies, aiding to isolate defective parts. In addition, applying vibration analysis and thermal imaging can uncover surprise issues, such as misaligned belts or overheating bearings, which are typically precursors to a lot more substantial failures.
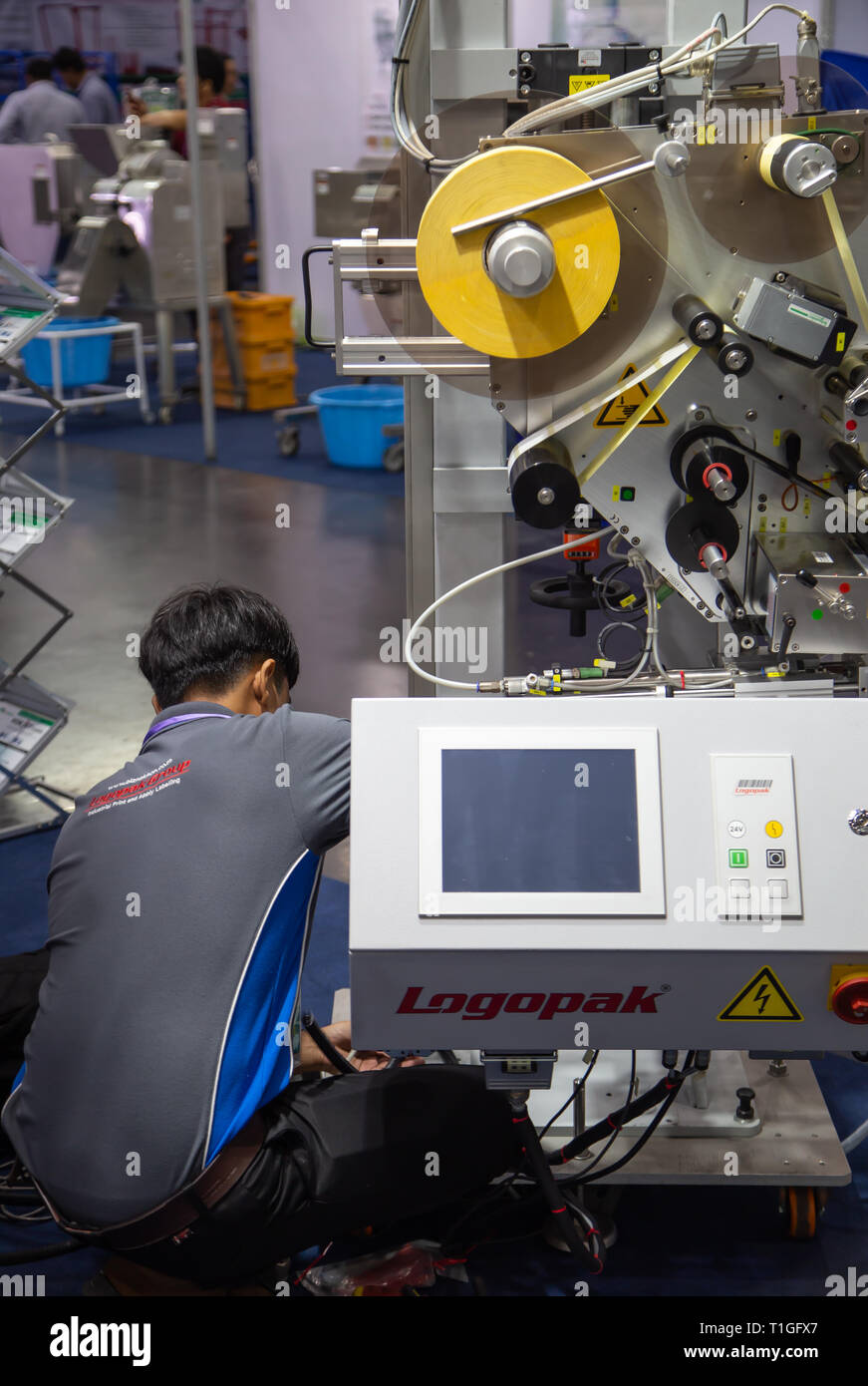
Step-by-Step Repair Service Treatments
A thorough repair work procedure is essential for bring back functionality to malfunctioning product packaging machines. The process begins with a detailed analysis of the problem, using analysis methods to determine the origin of the malfunction. Once identified, gather the needed devices and replacement parts to assist in the repair work.
Following, ensure that the machine is powered off and detached from its source of power to assure security throughout the repair work. Recording the machine's configuration before disassembly can help in reassembly - packaging machine repair service. Very carefully eliminate any panels or covers to access the malfunctioning parts, keeping in mind any details screws or bolts that require attention
Change or repair the malfunctioning components according to the maker's specs, making sure that all connections are safe and secure. After reassembly, conduct a visual inspection to confirm that all parts are appropriately installed and that there are no loose links.
When the device is rebuilded, reconnect the power and conduct tests to make certain appropriate performance. Screen the equipment during operation to identify any type of residual concerns.
Preventive Maintenance Practices
Keeping the performance of product packaging devices is not exclusively reliant on responsive repair treatments; proactive precautionary maintenance practices play a substantial function in ensuring their longevity and efficiency (packaging machine repair service). By implementing a structured preventive upkeep program, drivers can identify potential concerns before they escalate into pricey malfunctions
Technicians must consistently check components such as belts, gears, and sensors for wear and tear. Furthermore, cleansing equipments to get rid of dirt and particles is vital for optimum performance and to prevent contamination of products.
Educating personnel on correct use and handling of product packaging machines can also lessen the threat of operational mistakes that might bring about tools failing. Establishing a maintenance routine that consists of routine checks and substitutes of critical components can substantially prolong the lifespan of the equipment.
Recording all maintenance tasks not only aids in tracking the health and wellness of the equipment yet also adheres to regulatory standards. By prioritizing preventive maintenance, companies can ensure their packaging makers run at peak efficiency, eventually improving performance and reducing downtime.
Devices and Resources for Technicians
Outfitting service technicians with the right tools and sources is important for effective packaging machine repair service and maintenance. A well-stocked toolkit should consist of precision tools such as calipers, wrenches, and screwdrivers customized for certain equipment elements. In addition, analysis tools like multimeters and oscilloscopes enable professionals to identify electric concerns quickly and precisely.
Additionally, buying software remedies for devices surveillance can boost predictive maintenance practices. These applications assess equipment performance information, notifying specialists to possible concerns before they intensify.
Networking with peers and joining market forums can help with you could look here understanding sharing and best methods among technicians, promoting a collective environment for continuous understanding. Last but not least, preserving relationships with distributors ensures fast accessibility to extra parts and specialized devices, decreasing downtime during fixings. By leveraging these tools and resources, specialists can boost their performance and efficiency in keeping ideal performance of product packaging devices.
Conclusion
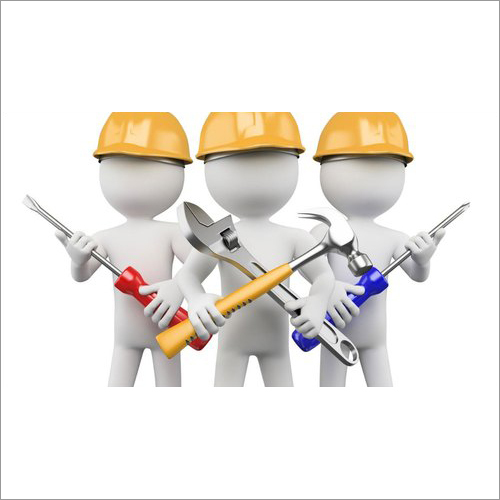
Efficient product packaging machine repair is essential for keeping operational continuity and item top quality in today's busy production atmosphere.Packaging makers, vital for efficient production lines, Go Here typically experience several typical issues that can interrupt operations.A detailed repair service procedure is vital for recovering functionality to malfunctioning product packaging equipments.Outfitting specialists with the right devices and sources is crucial for efficient packaging maker repair work and maintenance.In conclusion, efficient product packaging equipment repair work techniques are vital for keeping optimal performance and reducing operational downtime.
Comments on “Packaging Machine Repair Service: Guaranteeing Minimal Downtime and Optimum Effectiveness”